Design. Build. Fly.
What is Design Build Fly?
Design Build Fly (DBF) is an annual student competition organized by the American Institute of Aeronautics and Astronautics (AIAA). It challenges teams of university students to design, fabricate, and demonstrate the flight capabilities of an unmanned, electric-powered, radio-controlled aircraft to meet specific mission objectives. The competition typically includes:
Design Phase: Teams design their aircraft to meet the mission requirements specified in the competition rules. This involves extensive engineering analysis, including aerodynamics, structures, propulsion, and controls.
Build Phase: Teams construct their aircraft based on their designs. This phase often involves manufacturing and assembly techniques, materials selection, and system integration.
Fly Phase: Teams demonstrate the flight capabilities of their aircraft by performing various mission tasks. These tasks may include takeoff, landing, payload delivery, and endurance flights.
The competition is judged based on several criteria, including design report quality, aircraft performance, and mission success. DBF provides students with hands-on experience in aerospace engineering, project management, teamwork, and problem-solving, making it a valuable educational experience for aspiring engineers.
Design Build Fly 2024
Project Overview
In this project, I will explore Iowa State University's design, manufacturing, and testing of the aircraft Oliver for the 2024 American Institute of Aeronautics and Astronautics (AIAA) Design/Build/Fly (DBF) Competition. As a first-time team, we, Cyrannus, crafted the Oliver aircraft to compete in three flights and one ground mission to demonstrate Urban Air Mobility (UAM) capabilities.
The flight missions include:
Mission 1 (M1): A crew-only flight showcasing the aircraft's capabilities.
Mission 2 (M2): A medical transport mission where we aimed to maximize the plane's weight-carrying capacity for medical supplies.
Mission 3 (M3): An Urban Taxi Flight where we focused on maximizing the passenger count.
Additionally, the ground mission requires swiftly switching out payloads in a timed scenario. To meet these demands, we designed an ergonomic and accessible fuselage with easily removable medical supplies and passenger inserts for M2 and M3.
A key constraint for each mission is fitting the plane into a 2.5ft parking spot. We addressed this by developing a detachable wing mechanism allowing the wings to swivel. Our design considerations emphasized speed, payload carrying capacity, cargo space, and the innovative folding wing mechanism. Following an iterative design process, we continually improved our aircraft to meet these requirements.
The Oliver is a single-engine, low-wing taildragger with a conventional empennage. We selected a single engine to provide adequate thrust for all flight missions while reducing the required Watt-hours. The taildragger configuration offers a positive angle of attack on takeoff, aiding in achieving a takeoff within 20 ft. The curved belly fuselage was designed to house the battery and electronics while maximizing passenger space. The low-wing placement allows easy access to the payloads for each mission.
Through sensitivity analysis, we made informed mission-based design decisions. The aircraft can cruise at speeds up to 65 ft/s and is predicted to complete five laps in under 5 minutes. For M2, we plan to load the plane with 2 lb of medical supplies, and for M3, it can accommodate up to 45 passengers. Our successful flight tests have guided us in refining the design for the next prototype.
As a first-time team, this project has been a significant learning experience, showcasing our ability to design, build, and fly a competitive aircraft for the AIAA DBF Competition.
My Role
At Iowa State University, I held various roles throughout the AIAA Design/Build/Fly competition, each contributing to the project's success.
Initially, as Team Lead, I initiated the project in collaboration with the Make to Innovate program, our key stakeholders. My responsibilities included:
Project management.
Developing a comprehensive project charter (see image).
Establishing clear objectives and milestones.
I also created tests and deliverables to guide our progress and ensure alignment with our goals. To keep the team organized and on schedule, I developed a detailed Gantt chart (see Gantt chart image) outlining our timelines and deadlines.
Once we formally entered the competition, I transitioned into the Systems Integration Team Lead role, where I became heavily involved in the technical aspects of the aircraft. I conducted propulsion calculations using MotoCalc to optimize the aircraft's performance. I selected the motor, battery, and servos, ensuring their integration would meet the performance criteria. Additionally, I managed all internal wiring and carried out SolidWorks modeling to design the internal payload (see model images). Rapid prototyping was a crucial part of our development cycle, allowing us to refine our designs efficiently.

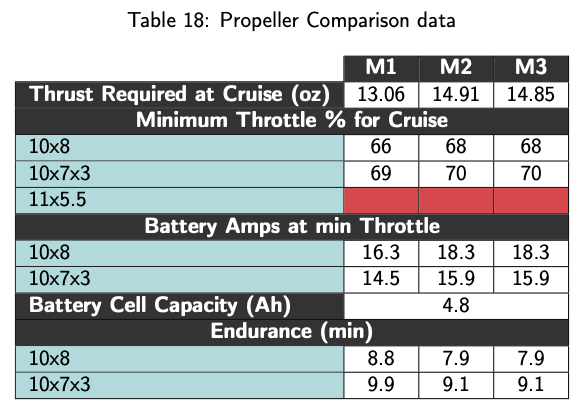
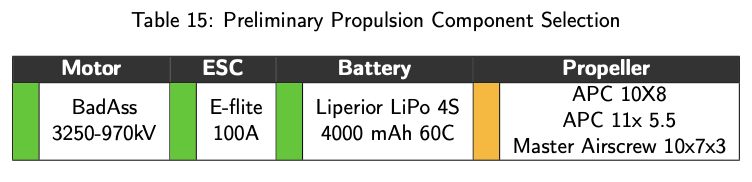

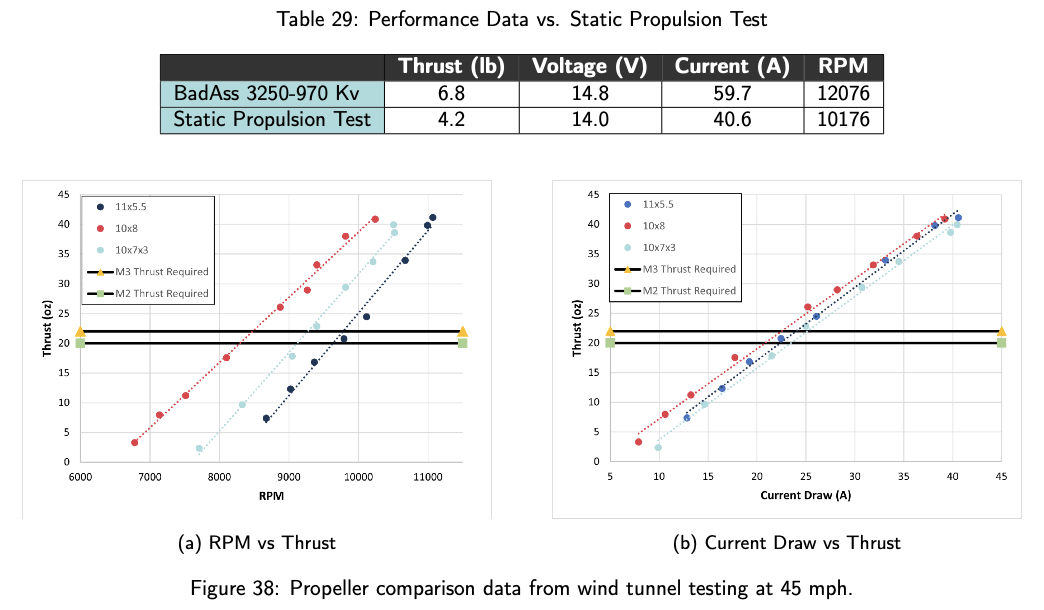
In my senior year, I took a lighter but still impactful role on the Operations Team, assisting first-year students in understanding the technical and organizational needs of the team. I contributed to planning and documentation efforts, spearheading the creation of essential documents in Overleaf and writing them in LaTeX (see document samples). This documentation ensured that all project work was well-organized and accessible. Furthermore, as the trip coordinator, I organized our team's travel to Wichita, KS, for the competition's flyoff, managing logistics and team coordination.
Safety Documents
Test Flight Documentation
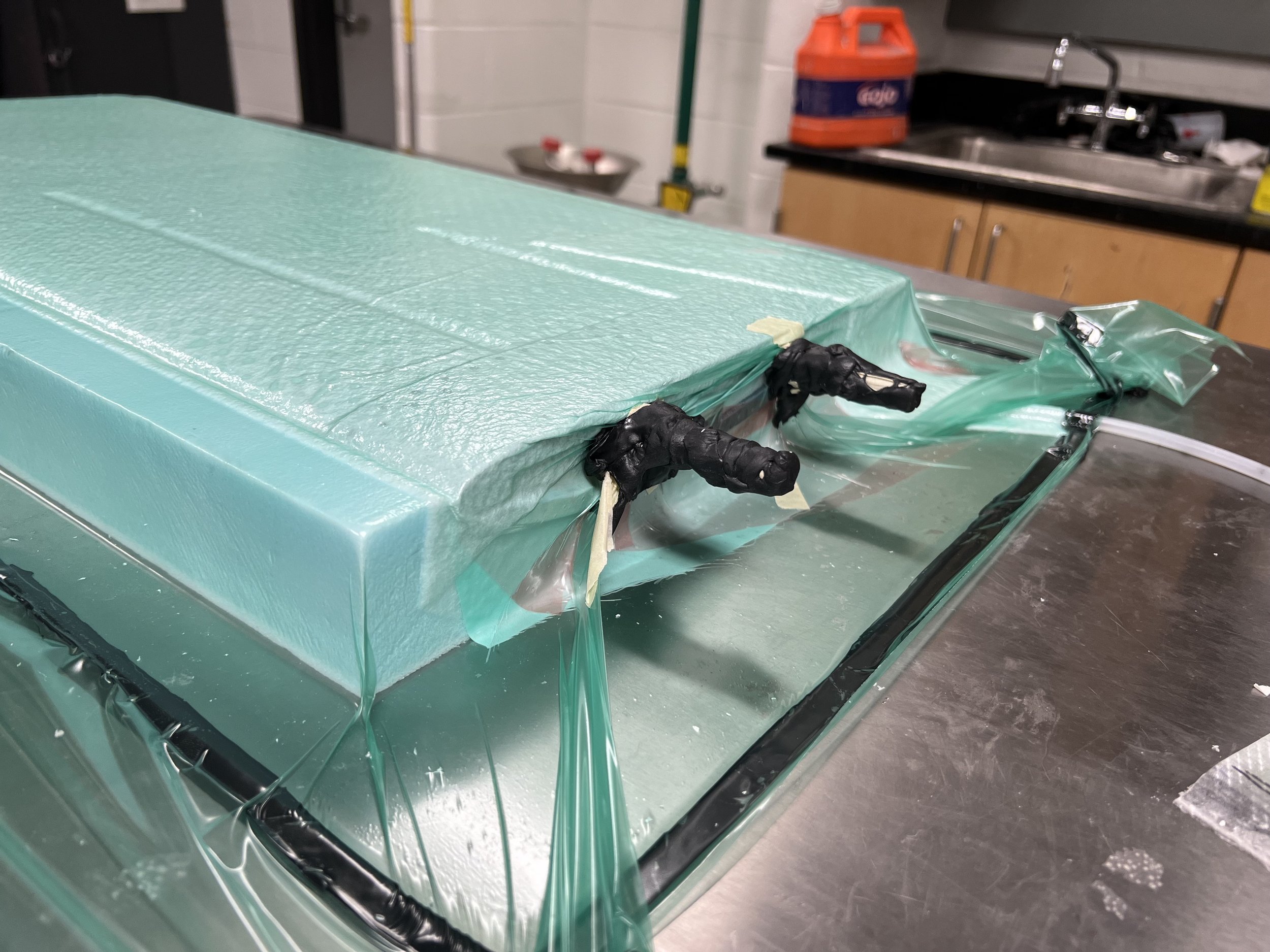
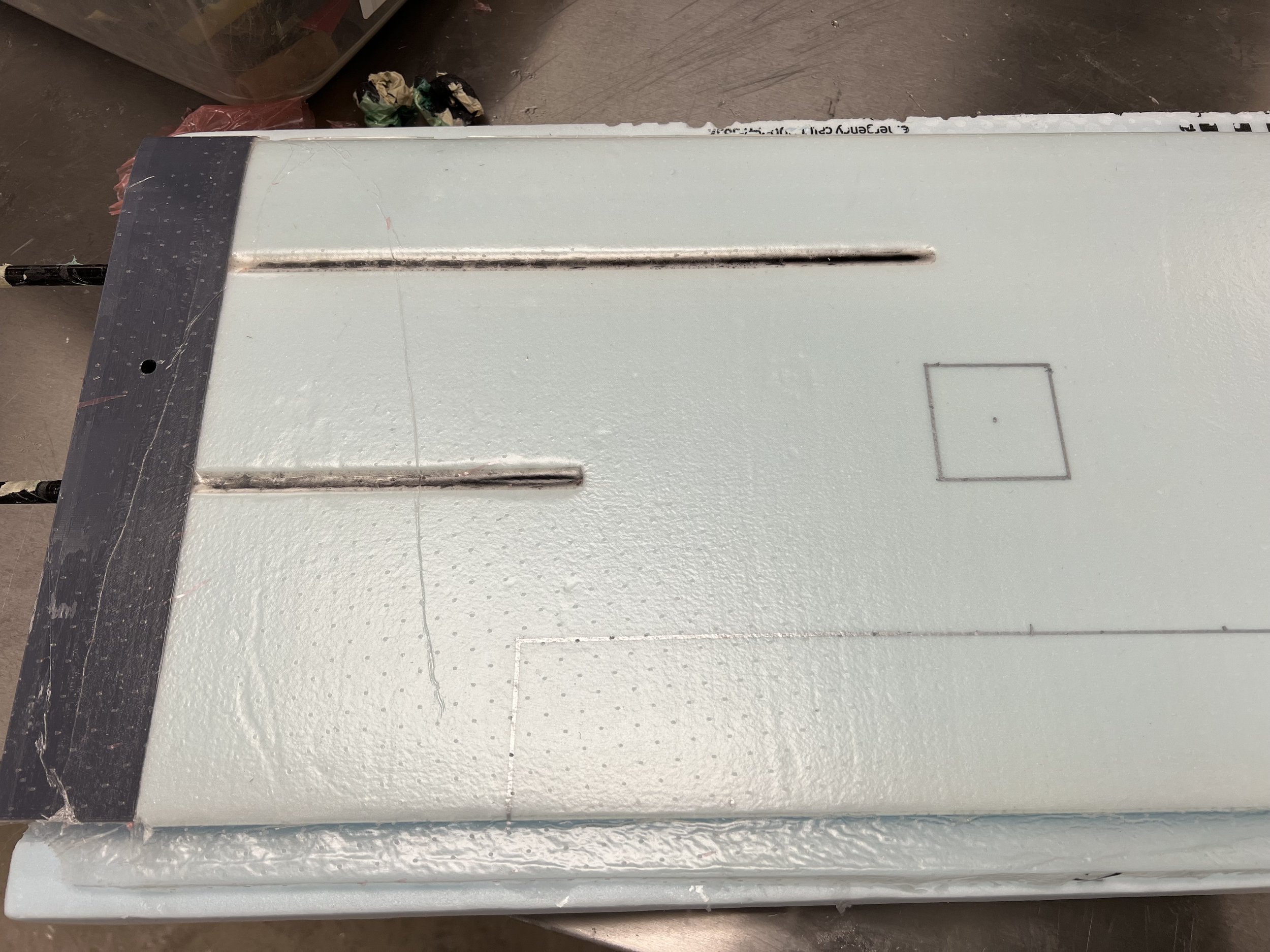
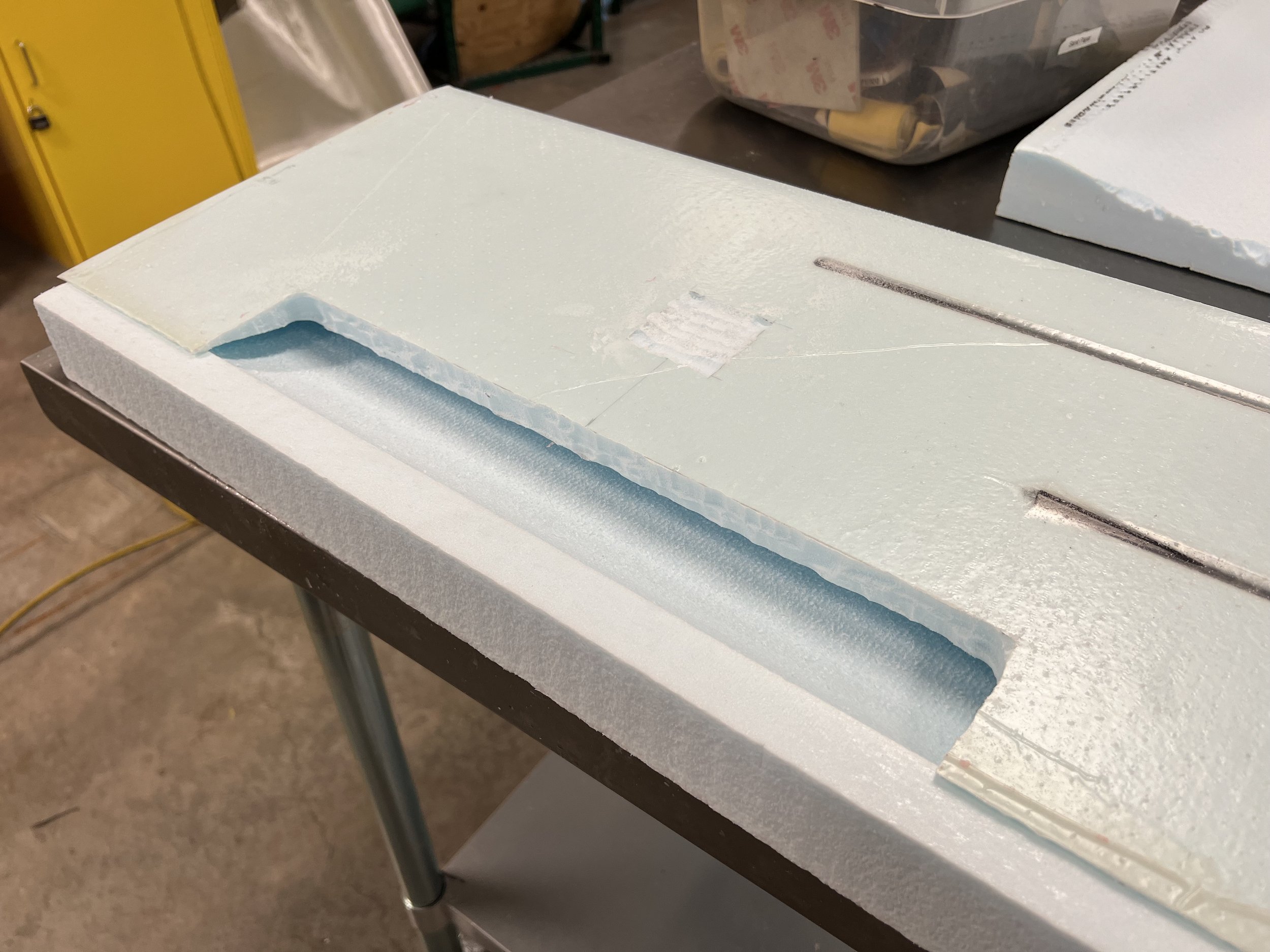
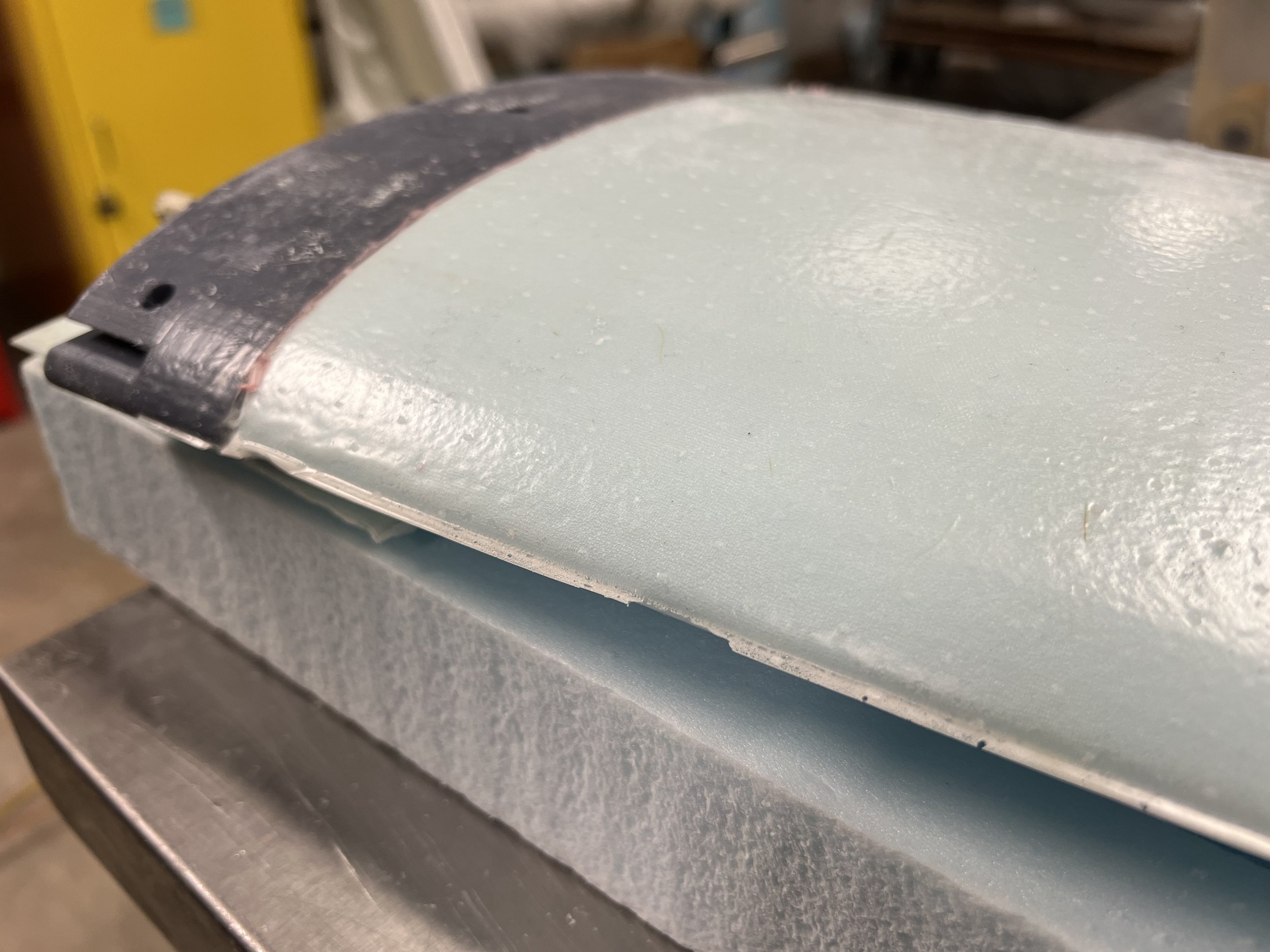
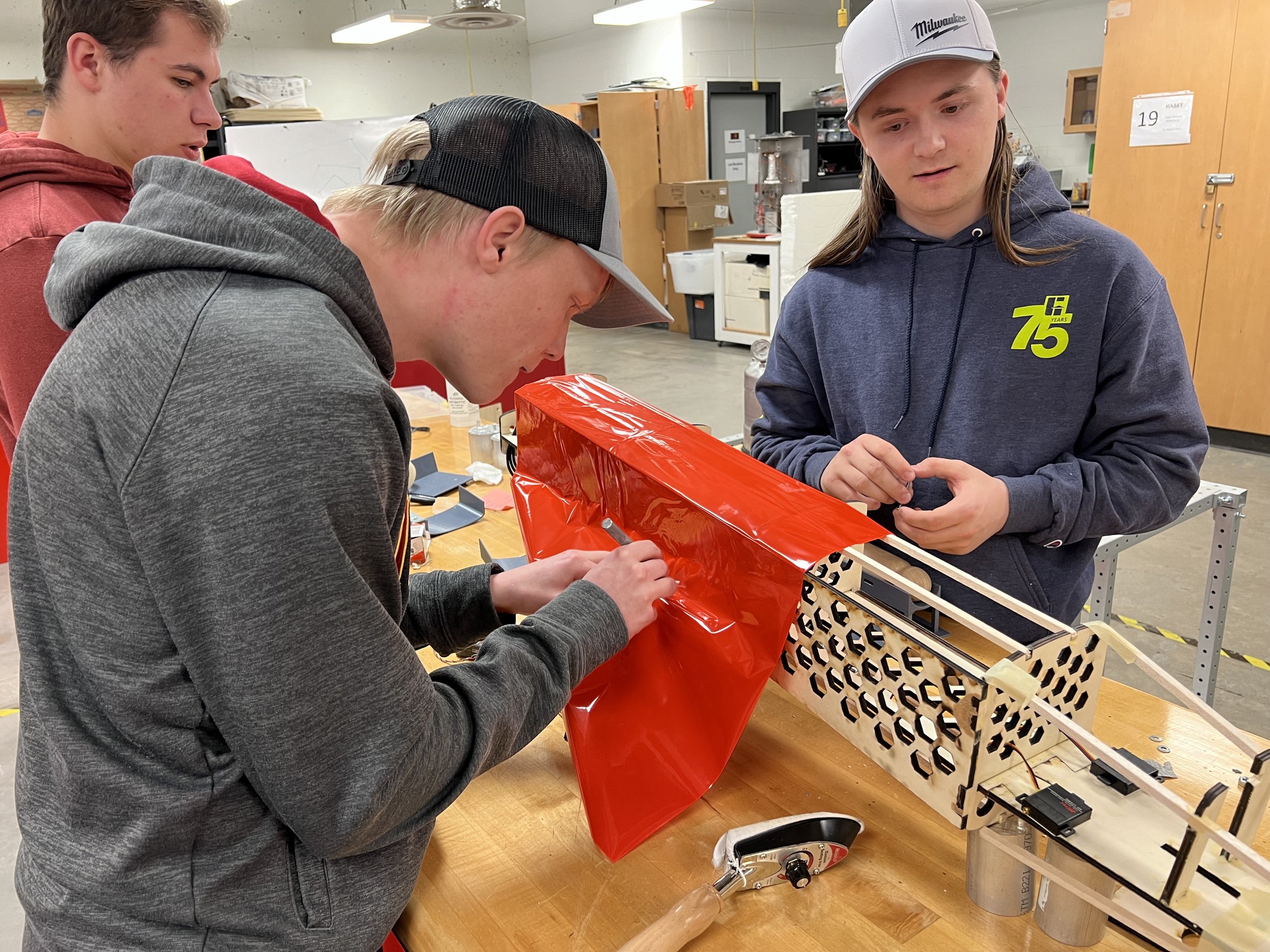
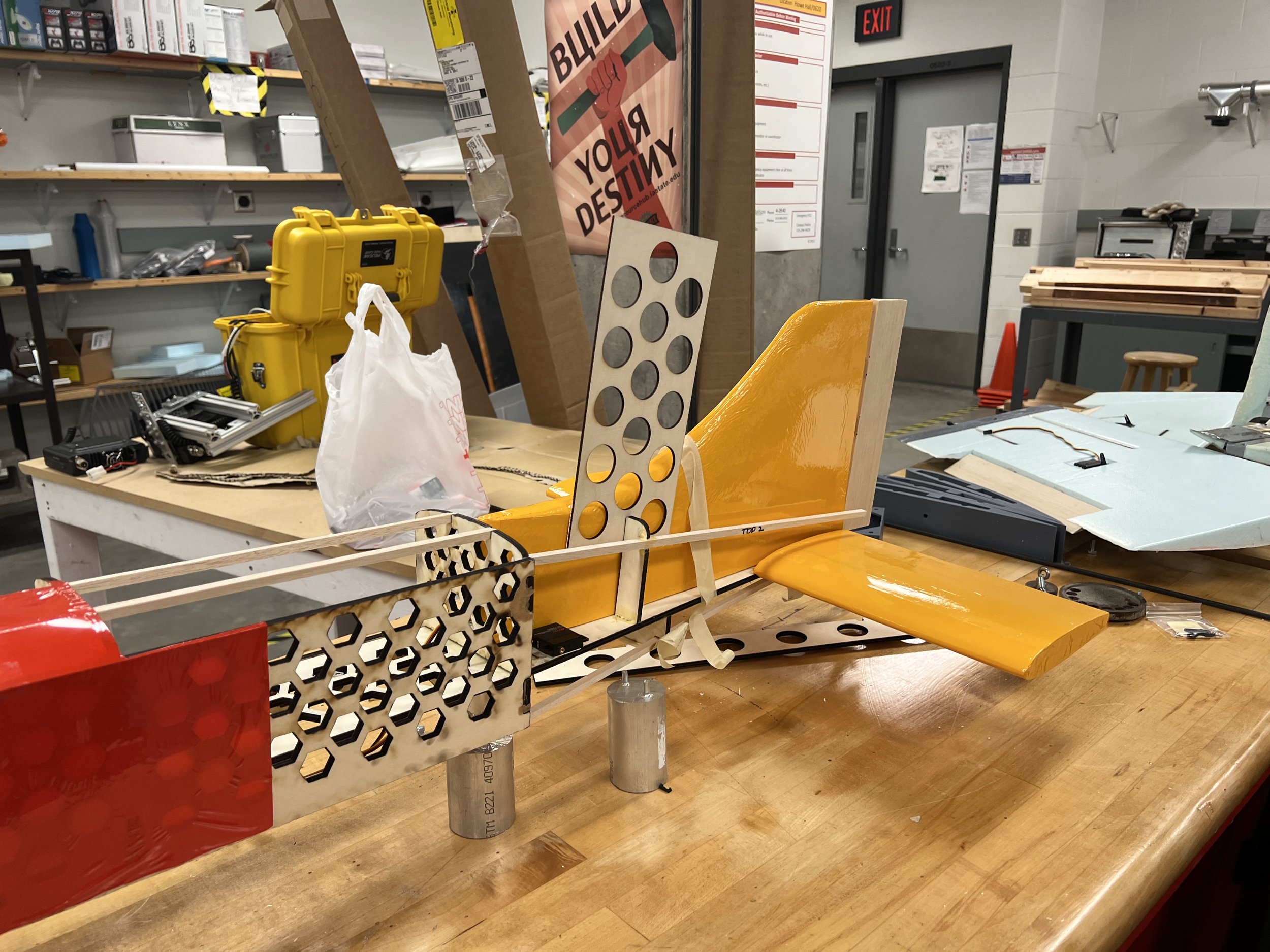

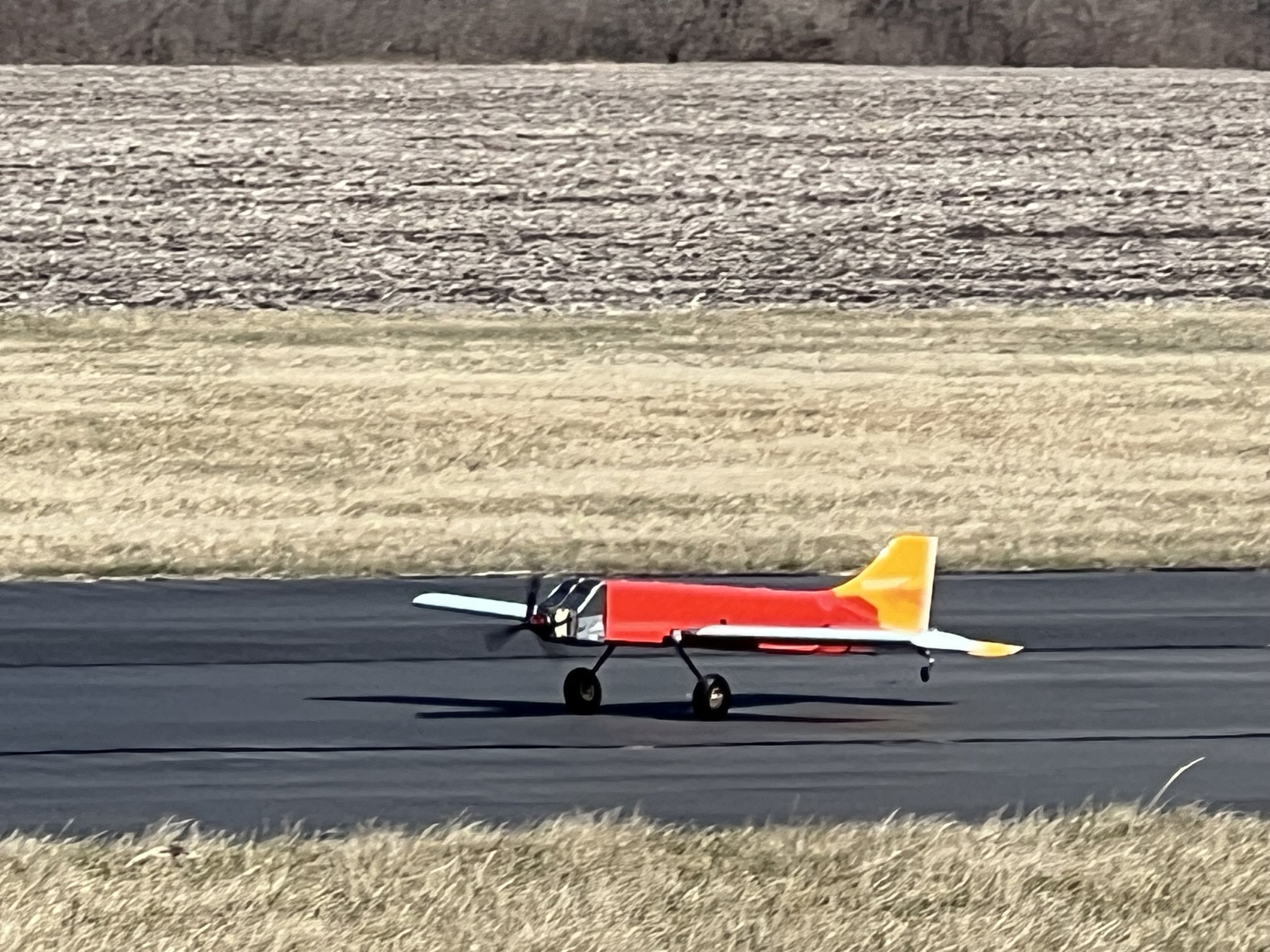
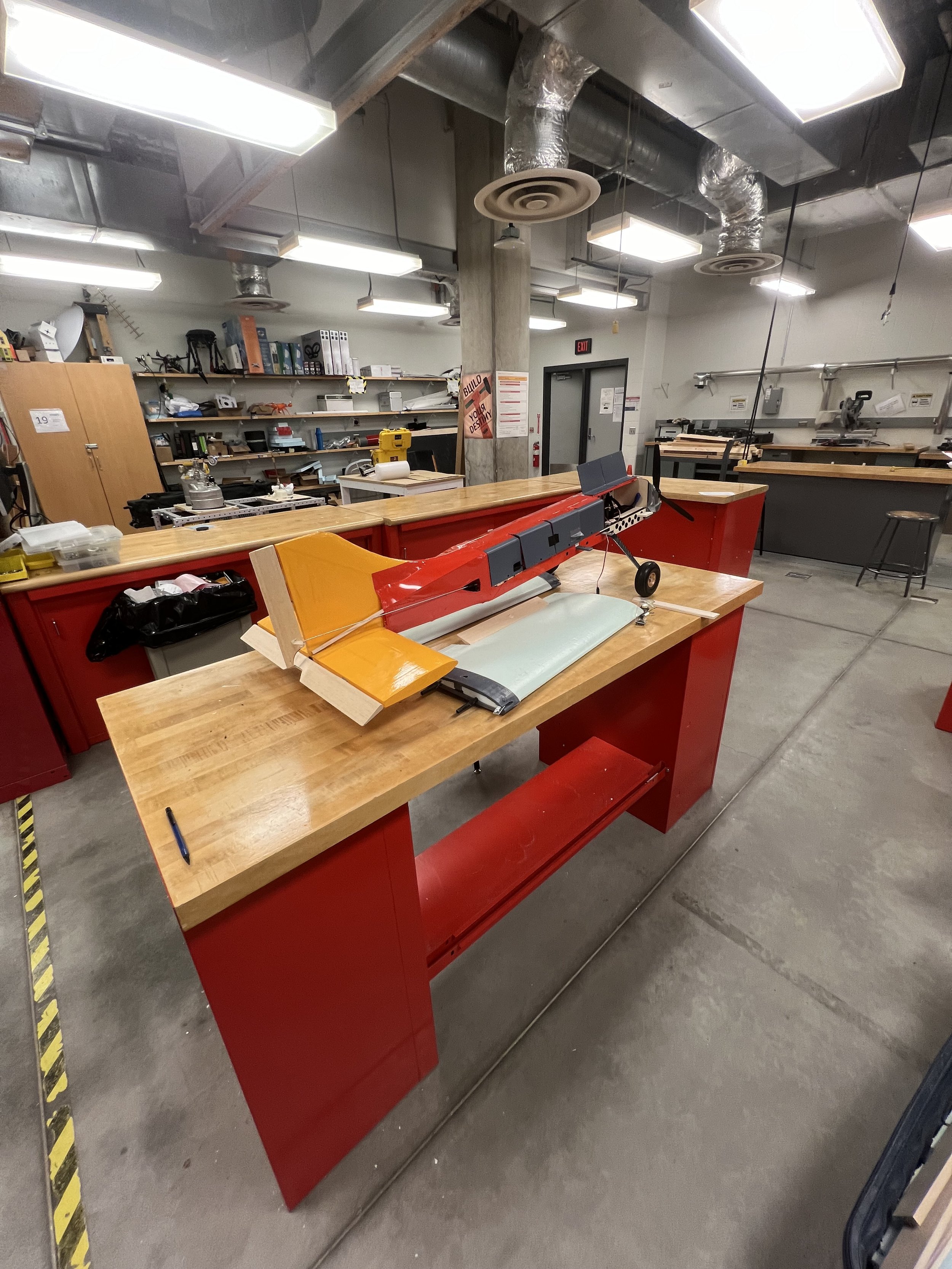
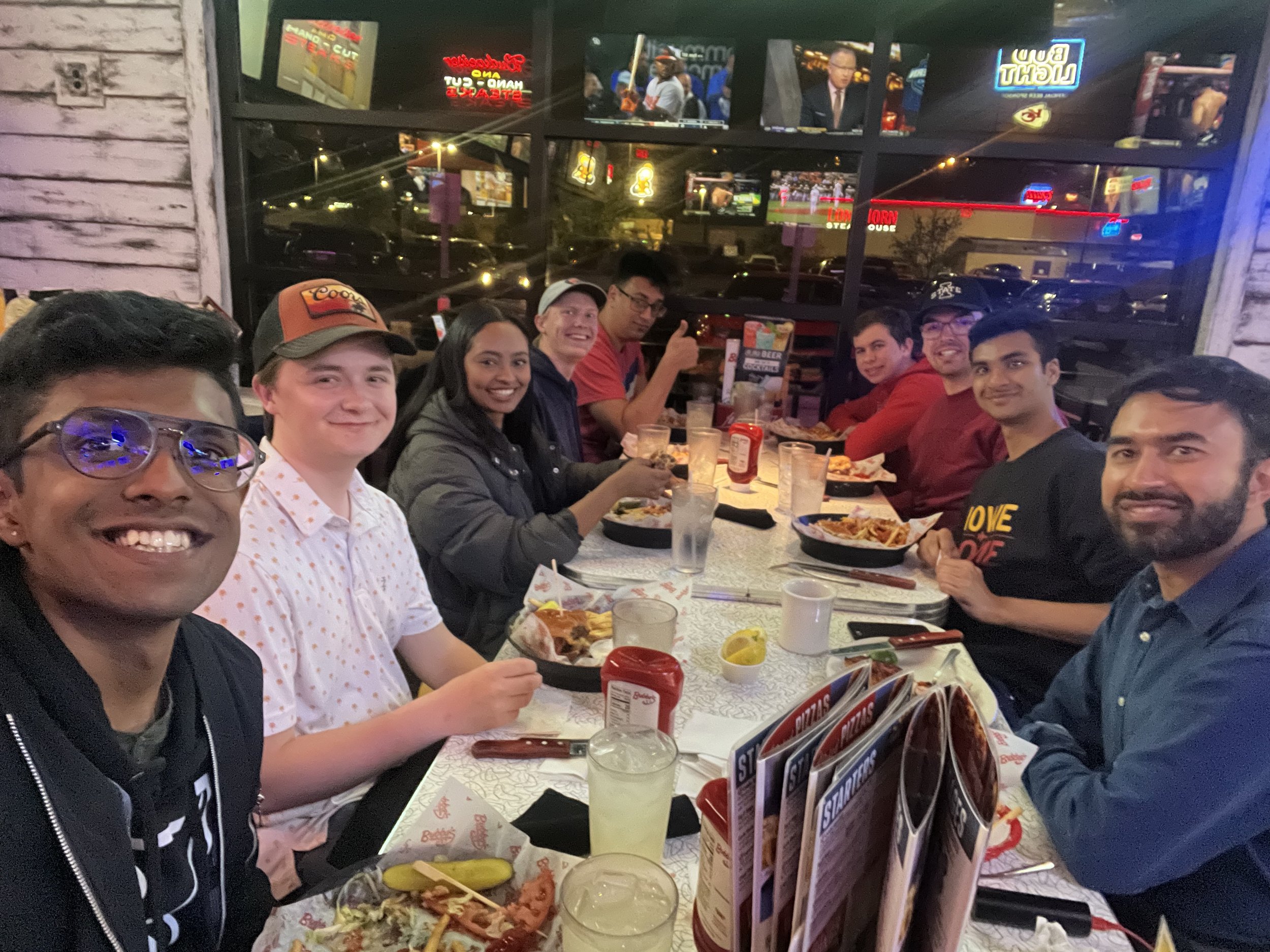
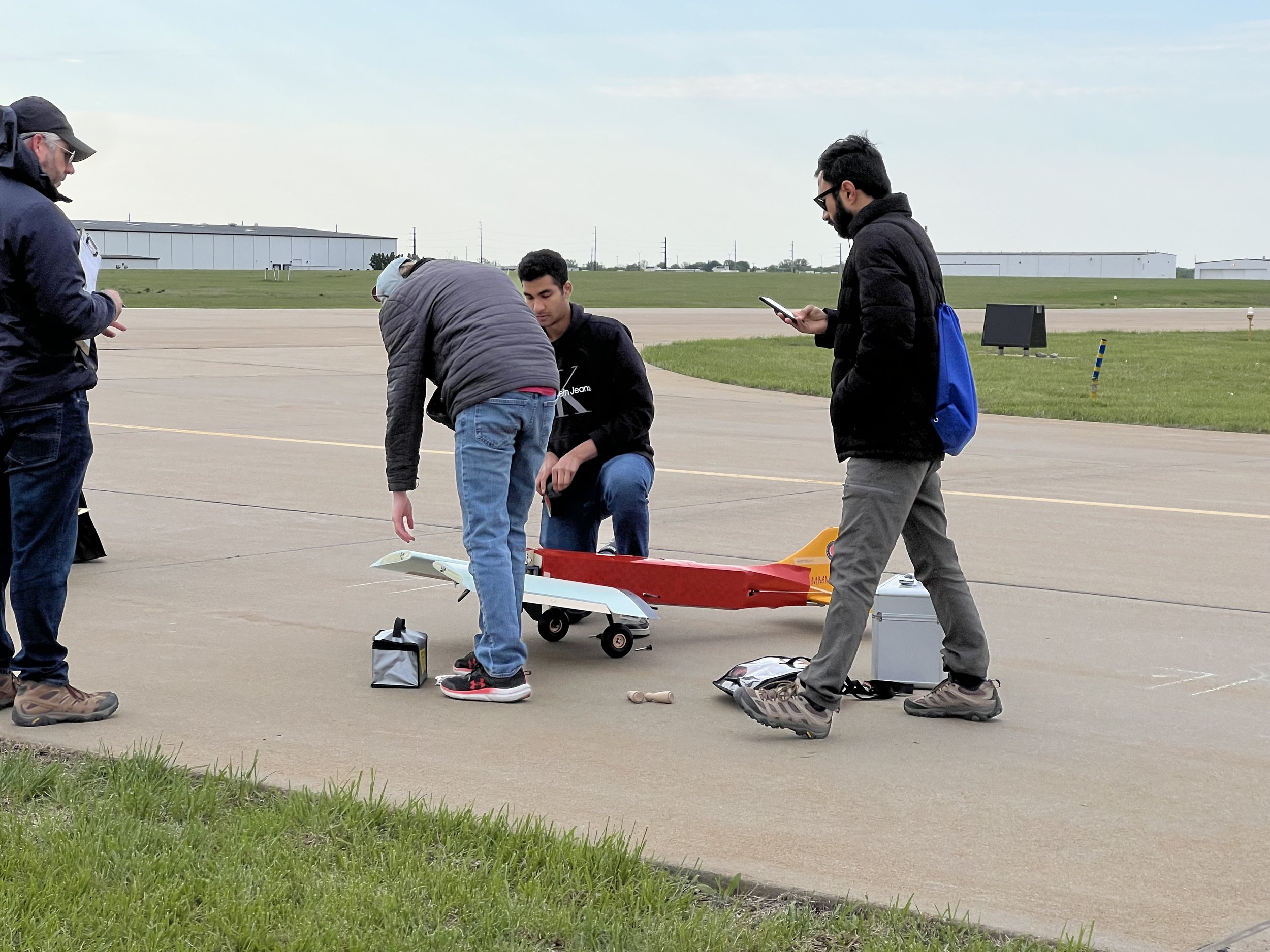
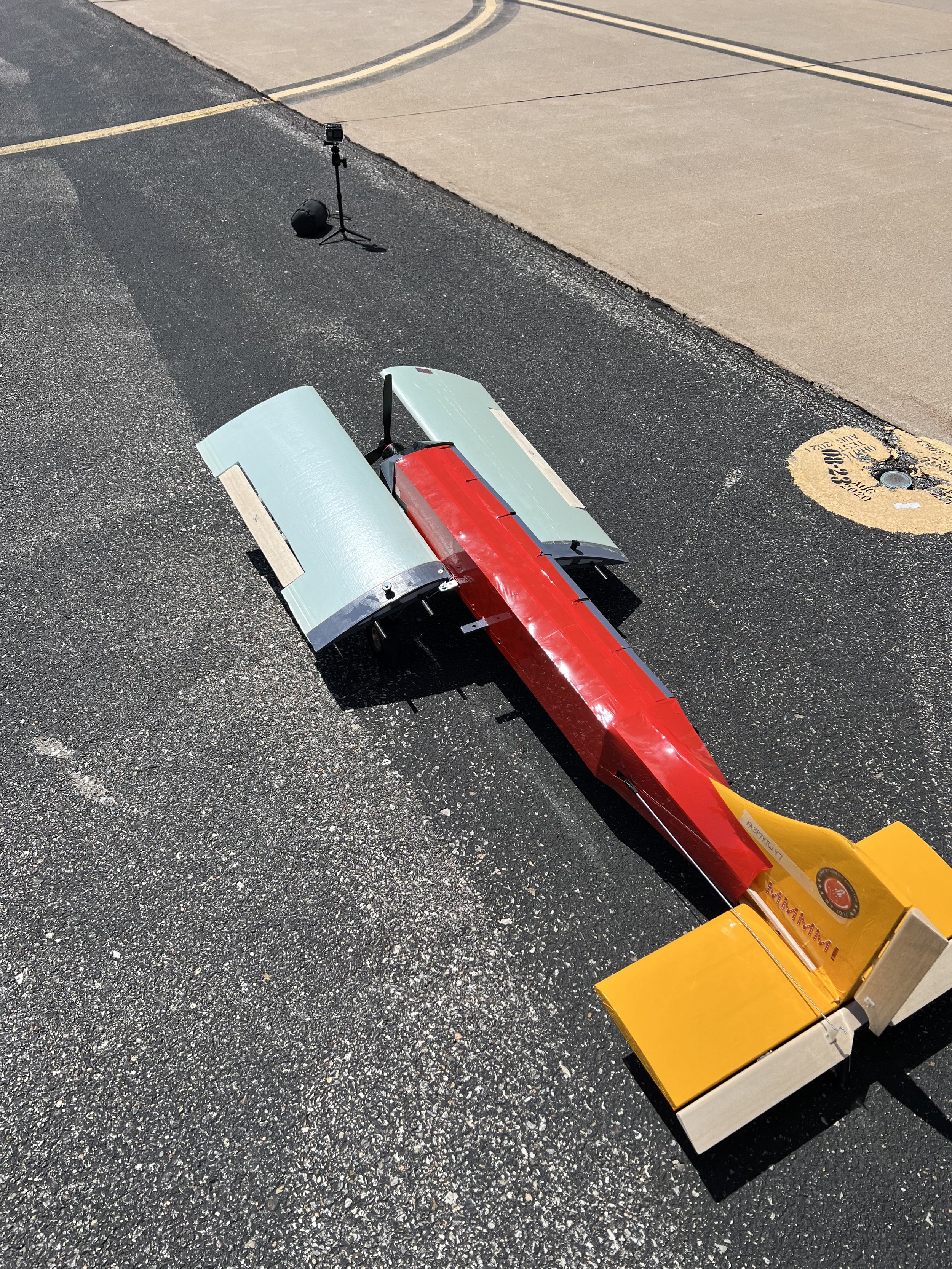